Molycop is continuing to develop standards for its manufacturing of wheels with a focus on sustainable practices.
Key Facts
- Molycop traces its support of Australia’s heavy haul sector back to the 1980s.
- The work Molycop has done to maximise the efficiency and strength of rail wheels has benefited the entire rail industry.
- Molycop has turned its attention to research and development of wheels that will support the next generation of locomotives, passenger cars and freight rollingstock.
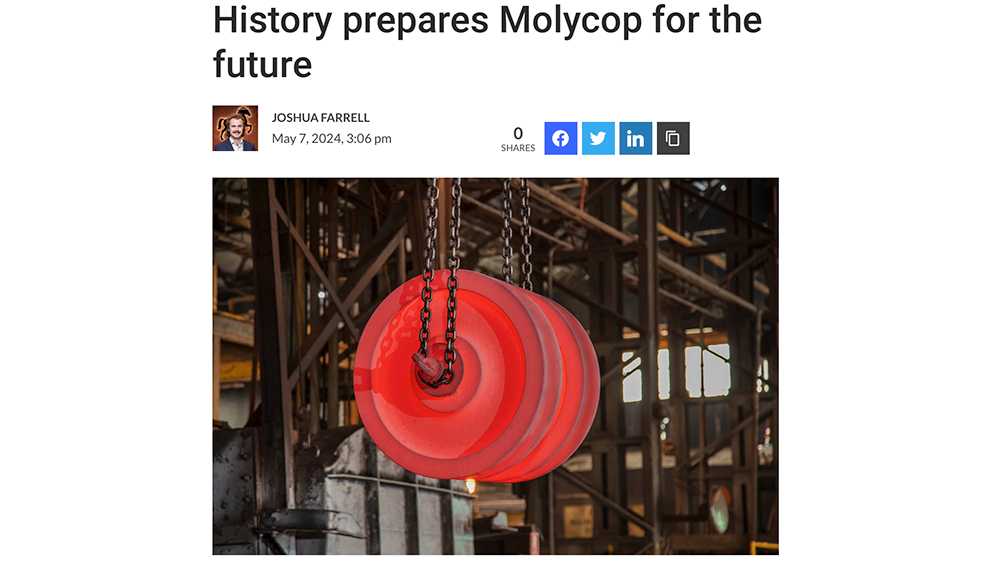
Molycop now comprises 15 major operational sites in Africa, Australia, Canada, Chile, Indonesia, Mexico, Peru, Spain and USA supported by local sales, service and distribution presence.
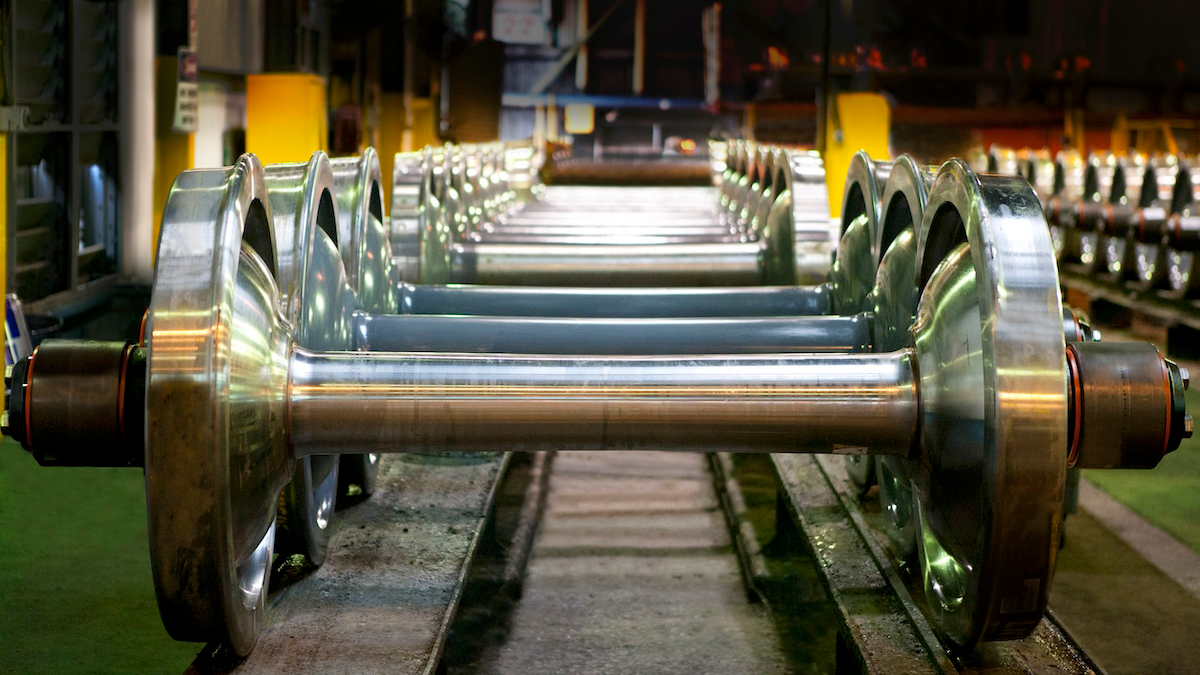
“When we first started with a focus on heavy haul, it was about pushing the nominal axle load from 25 tonnes through to 35 and now up to 42 tonnes,” Forbes said. “Australia has the heaviest haulage in the world, and I think a lot of that was off the work we did developing these wheels in conjunction with the industry.”
Forbes said that the development occurred in two phases. It started with improving the plate design to maximise the efficiency and the strength of the wheel.
Once Molycop had improved this design they then released the design to the broader industry.
Forbes explained that as Molycop had worked closely with industry to develop these improved wheels, it wanted to give it back to the sector.
“The second phase of the development was improving the materials we were using,” he said. “We began pushing what we were doing to make our wheels far exceed the specs that were required by the Association of American Railways. By doing this it improved interoperability and safety for users.”
Collaboration is key
Molycop has been operating for more than 100 years and owes this to the collaboration it has maintained throughout its existence. The organisation has always collaborated with university and institutes, but Forbes believe the success lies in its association with other collaborators.“We have always been industry led,” he said. “We help them with challenges Instead of telling industry what it needs, we listen to what is required and design a product to meet these needs.
“We always seek to understand the problem first and then design the solution for that specific problem.”
Sustainability in practice
Molycop is continuing to develop standards for its manufacturing of wheels with a focus on sustainable practices. The company is currently reporting and tracking its Greenhouse gas (GHG) Emissions annually for Scope 1, 2 and 3.“With a focused and measured approach to a lower carbon operating model, we are well placed to support our customers on the journey to a more sustainable future,” Forbes said.
“With a history of more than 106 years, our products have been at the forefront of many transitions in the rail and manufacturing industries.
“Supporting our customers and leading our own transition across the century, the challenge has been accepted on this new evolution and we have the right team in place to make it happen.”