Flotation is a critical but frequently underestimated stage in mineral processing. Molycop’s Advanced Process Control Manager, Kobus Oosthuizen, understands what common mistakes are made and how to avoid them.
Key Facts
- Molycop’s flotation solution uses real-time camera and machine vision technology to eliminate reliance on slow, manual froth inspections.
- Advanced multivariable controllers improve stability, reduce startup times and cut tailings losses.
- Molycop’s integrated reagent monitoring and froth analytics let operators fine-tune chemical dosing, boosting recovery and efficiency while avoiding trial-and-error.
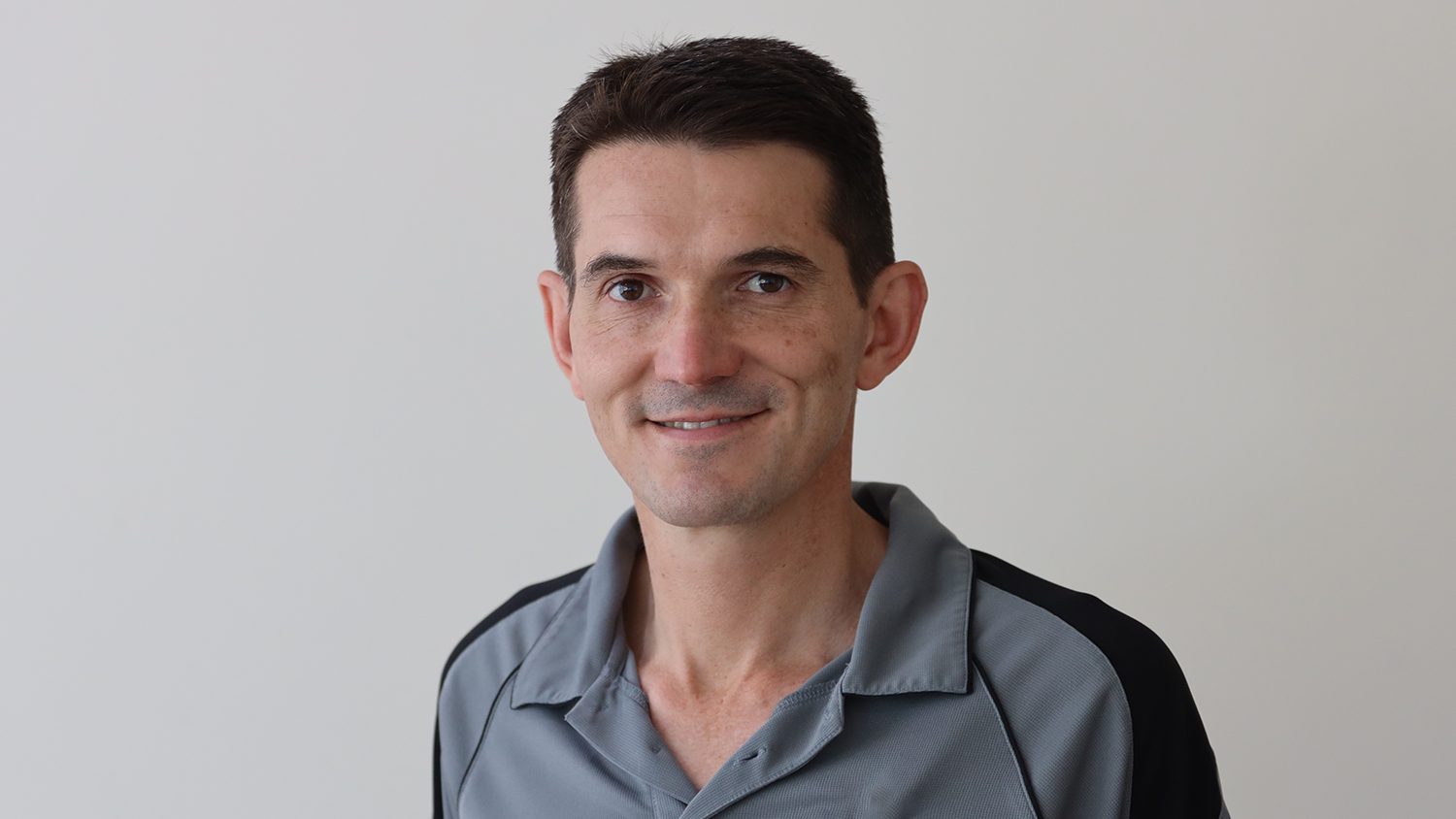
Kobus explains there are three common mistakes plants make – and outlines how to avoid them:
1. Relying on periodic visual checks
The mistake
Many operations still rely on manual froth inspections carried out once or twice a shift. These checks, while useful, offer only a snapshot in time and often miss the subtle, rapid changes occurring in the cell.
The Molycop solution
Flotation conditions can shift within minutes, making real-time visibility critical. Molycop’s flotation solution uses advanced camera technology and machine vision algorithms to track froth characteristics continuously and take appropriate corrective action when required. This data is processed in real-time to support timely decisions and deliver consistent control across the circuit.
2. Ignoring multivariable interactions and circulating streams
The mistake
Basic Proportional-Integral-Derivative (PID) controllers are often used to control individual flotation cell levels – sometimes including a feed-forward term. While PID- and feed-forward controllers are well-proven technologies in industry, the performance of these strategies deteriorates rapidly when slow dynamics and delayed responses (due to residence times in flotation cells) are not adequately accounted for.Cleaning circuits with circulating streams are particularly vulnerable to sustained oscillations. While simple SISO control strategies may appear to give reasonable stability, their limitations are often exposed when operating points are changed as part of a mass-pull or grade control strategy.
The Molycop solution
Molycop’s flotation solution is implemented in a hierarchical fashion, focusing on stability as a first layer – using a multivariable controller implementation. Stabilisation alone often results in an increase in recovery (at a desired grade). Advanced stabilisation also reduces startup times significantly.
Results have been published where the time since starting up the flotation circuit until concentrate and tailings grades reach their desired operating ranges were reduced to less than half the original times – leading to a significant reduction in tailings losses to the client.
Once the stabilisation layer is in place, more advanced mass-pull, grade control and machine vision-based strategies can be customised as subsequent layers to meet the unique requirements of each implementation, all without compromising overall system stability.
3. Overlooking the impact of reagent changes
The mistake
Reagents are often treated as static inputs or controlled in a fixed ratio to the flotation feed. Operators may not fully account for how slight changes in dosage or type in one flotation section can affect froth behaviour and, ultimately, recovery.
The Molycop solution
Molycop’s system enables reagent dosage monitoring in tandem with visual froth analytics. By correlating reagent trends with froth characteristics, plants can move beyond assumptions to truly understand how chemical interactions shape performance. This level of insight helps eliminate trial-and-error approaches, leading to better recovery and reagent efficiency.